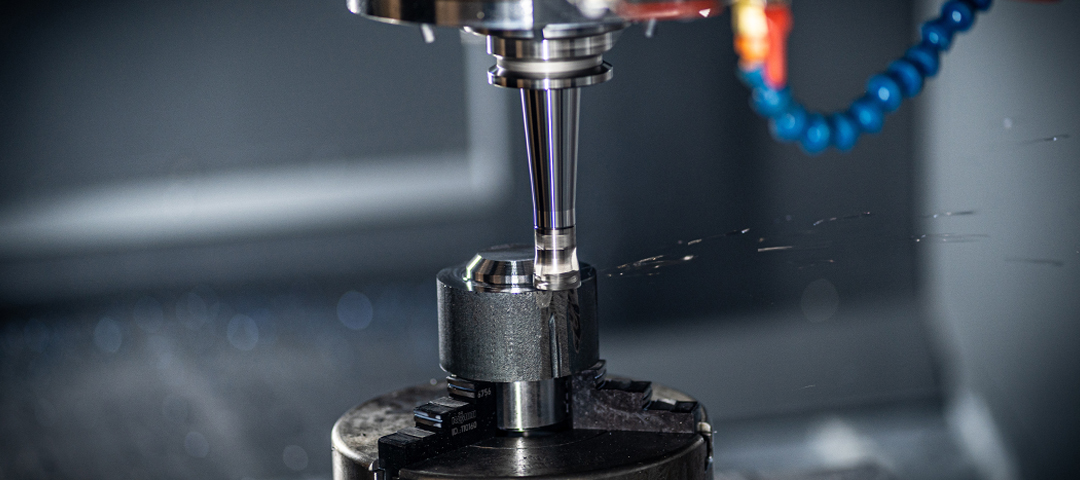
CNC machining: manufacturing and design guidelines
CNC machining is a manufacturing process that is carried out through computer-controlled CNC machine tools. In CNC machining, computer programs control the movement and operation of machine tools through pre programmed instructions to achieve precise machining of parts. This article will provide you with some manufacturing and design guidelines for CNC machining.
Manufacturing Guidelines
Part design
Before conducting CNC machining, it is necessary to first design the parts. Designers should consider the capabilities and limitations of CNC machine tools and design part geometries that meet processing requirements.
Material selection
Choosing materials suitable for CNC machining is very important. Some common CNC machining materials include metal alloys, plastics, wood, etc. Select appropriate materials according to the requirements of the parts to ensure machining quality and performance.
Manufacturing process planning
It is necessary to develop a detailed process plan before conducting CNC machining. The plan should include processing sequence, cutting parameters, clamping methods, etc., to ensure that the parts can be processed as expected.
Writing machining programs
The machining program is the core of CNC machining. By writing machining programs, the geometric information of the parts is transformed into instructions that the machine tool can understand, in order to control the movement and operation of the machine tool.
Process Control
During CNC machining, process monitoring and control are required. By real-time monitoring of parameters during the machining process, such as cutting force, cutting temperature, etc., machining parameters can be adjusted in a timely manner to improve machining quality and efficiency.
Design Guidelines
Design geometric shapes
When designing CNC machining parts, geometric shapes should be simplified as much as possible to avoid complex curves and sharp inner and outer corners. This will help improve machining accuracy and reduce processing time and costs.
Consider processing sequence
When designing CNC machining parts, the rationality of the machining sequence should be considered. Try to break down the processing process into simple steps to avoid increasing processing difficulty and cost due to unreasonable processing sequence.Avoid excessive cutting: When designing CNC machining parts, excessive cutting should be avoided as much as possible. Excessive cutting can lead to material waste and increased processing time. Reasonably select cutting tools and parameters to minimize cutting volume.
Consider clamping methods
When designing CNC machining parts, the rationality and feasibility of clamping methods should be considered. Choose appropriate fixtures and fixture positions to ensure the stability and accuracy of the parts during the machining process.
Consider process requirements
When designing CNC machining parts, the rationality and feasibility of process requirements should be considered. Such as surface smoothness, dimensional tolerances, etc. Communicate fully with manufacturers and operators to ensure that the design meets the actual processing requirements.
The manufacturing and design guidelines for CNC machining include aspects such as part design, material selection, manufacturing process planning, machining program writing, and machining process control. Reasonable manufacturing and design guidelines can improve the efficiency and quality of CNC machining, ensuring that parts can be processed as expected.
CNC (Computer Numerical Control) machining can be used to process soft metal materials. Soft metals typically refer to metals with lower hardness and higher plasticity, such as aluminum, brass, and copper. Here are some important precautions for handling soft metals in CNC machining:
Choose suitable cutting tools: For soft metal materials, high-speed drills, blades, and milling cutters are usually used. These cutting tools are capable of working at higher speeds and effectively cutting and cutting soft metals.
Control cutting parameters: In the processing of soft metals, it is necessary to adjust cutting parameters based on the specific material's hardness and plasticity. These parameters include cutting speed, feed rate, and cutting depth. Appropriate cutting parameters can ensure the efficiency and quality of machining.
Using appropriate coolant: As soft metals are prone to high temperatures during processing, it is important to use appropriate coolant. Cooling fluid can lower the temperature of the machining area, reduce the risk of tool wear and material deformation, and improve the quality of the machining surface.
Maintaining stable clamping: Soft metals are often relatively soft during processing, so appropriate fixtures and clamping methods are needed to ensure the stability of the workpiece. This helps to avoid vibration and deformation during the machining process.
Proper post-treatment: Soft metals usually require appropriate post-treatment, such as deburring, polishing, and coating. These post-processing steps can improve the surface smoothness and overall quality of the final product.
CNC machining of soft metals requires the selection of appropriate cutting tools, adjustment of cutting parameters, use of coolant, stable clamping, and appropriate post-processing. These steps help to obtain high-quality and accurate machining results.