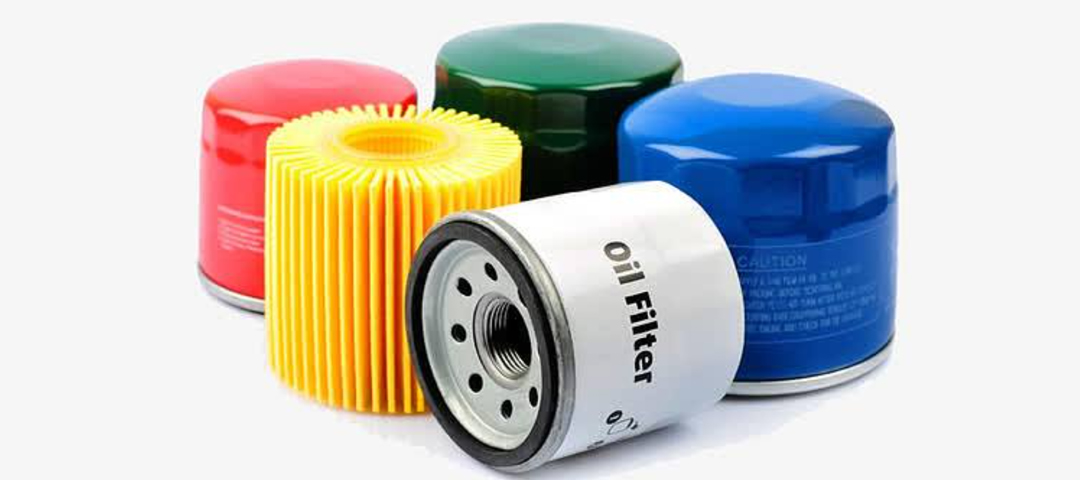
The benefits of using plastic injection molding in automotive manufacturing
Plastic injection molding is a widely used plastic manufacturing process used for large-scale production of various plastic products. It is the process of injecting molten plastic into a mold under high pressure, then cooling and solidifying in the mold to obtain the required plastic products.
Plastic injection molding type
Dual color/multi color injection molding
Using two or more plastic materials with different colors or characteristics, inject them into the mold simultaneously through a special injection machine and mold to obtain products with multiple colors or characteristics.Embedded injection molding
During the injection molding process, materials are embedded into plastic products to achieve the manufacturing of composite materials.High speed injection molding
Utilize high-speed injection machines and optimized injection processes to accelerate injection speed and improve production efficiency and yield.Thin wall injection molding
For manufacturing thin-walled plastic products, such as plastic containers, boxes, cups, etc., special mold design and injection processes are required to ensure the filling and cooling of thin-walled parts.High temperature/high pressure injection molding
Suitable for thermoplastic materials, requiring high-temperature and high-pressure injection processes to ensure the melting and filling performance of plastic materials.Precision injection molding
For manufacturing high-precision and high demand plastic products, such as optical lenses, medical devices, electronic products, etc., precision molds and injection processes are required.Large injection molding
Suitable for large-sized plastic products, such as automotive parts, large containers, etc., requiring a large injection machine and powerful injection force.
The benefits of using plastic injection molding in automotive manufacturing
Light weight
Plastic injection molding can produce lightweight automotive components. Compared to traditional metal components, plastic components are lighter in weight, helping to reduce the weight of the vehicle, improve fuel efficiency, and reduce exhaust emissions.
High cost-effectiveness
Plastic injection molding has lower costs compared to other manufacturing methods. Injection molding can achieve large-scale mass production, improve production efficiency, and reduce production costs.
Strong design flexibility
Plastic injection molding can achieve complex shapes and detailed design of automotive components. Injection molding can manufacture various shapes, sizes, and surface textures of parts according to product design requirements, meeting the creativity and needs of automotive designers.
Reducing noise and vibration
Plastic components have good sound absorption and shock absorption performance, which can reduce noise and vibration during car driving and improve ride comfort.
Good corrosion and wear resistance
Some plastic materials have excellent corrosion and wear resistance, which can cope with harsh environments and long-term use, improving the lifespan and durability of automotive components.
Reducing manufacturing complexity
Plastic injection molding can manufacture composite components of multiple components, reducing the joints and connections between components, and reducing manufacturing complexity and assembly difficulty.
Recyclable
The waste from plastic injection molding can be recycled and reused, reducing resource waste and environmental pollution.
Solutions for Automotive Injection Molding
Choose materials suitable for automotive injection molding
Common automotive injection molding materials include polypropylene (PP), polyethylene (PE), polycarbonate (PC), polyamide (PA), etc. Select materials with sufficient strength, wear resistance, corrosion resistance, and high temperature resistance according to the requirements of the components.Component design optimization
Considering the fluidity, shrinkage, and extrusion force of the material, optimize the design of geometric shape, wall thickness, holes, chamfers, and other aspects to ensure the filling, cooling, and strength requirements during injection molding.High quality mold manufacturing
The mold should be accurately designed and manufactured based on the shape and size of the components. Ensure that the mold has a good cooling system to improve injection molding efficiency and product quality.Control injection molding process parameters
Including the control of parameters such as injection temperature, injection pressure, injection speed, and cooling time. Through reasonable process control, ensure uniform filling and sufficient cooling during the injection molding process, and reduce defects such as bubbles, warping, and shrinkage.Ensure product quality meets requirements
By using advanced quality inspection equipment and methods such as coordinate measuring machines, tensile testing machines, impact testing machines, etc., the dimensions, physical properties, surface quality, and other aspects of components are tested and verified.Provide comprehensive after-sales service
This includes product quality assurance, repair, and replacement to meet customer needs and address potential issues.